Turning invisible light visible
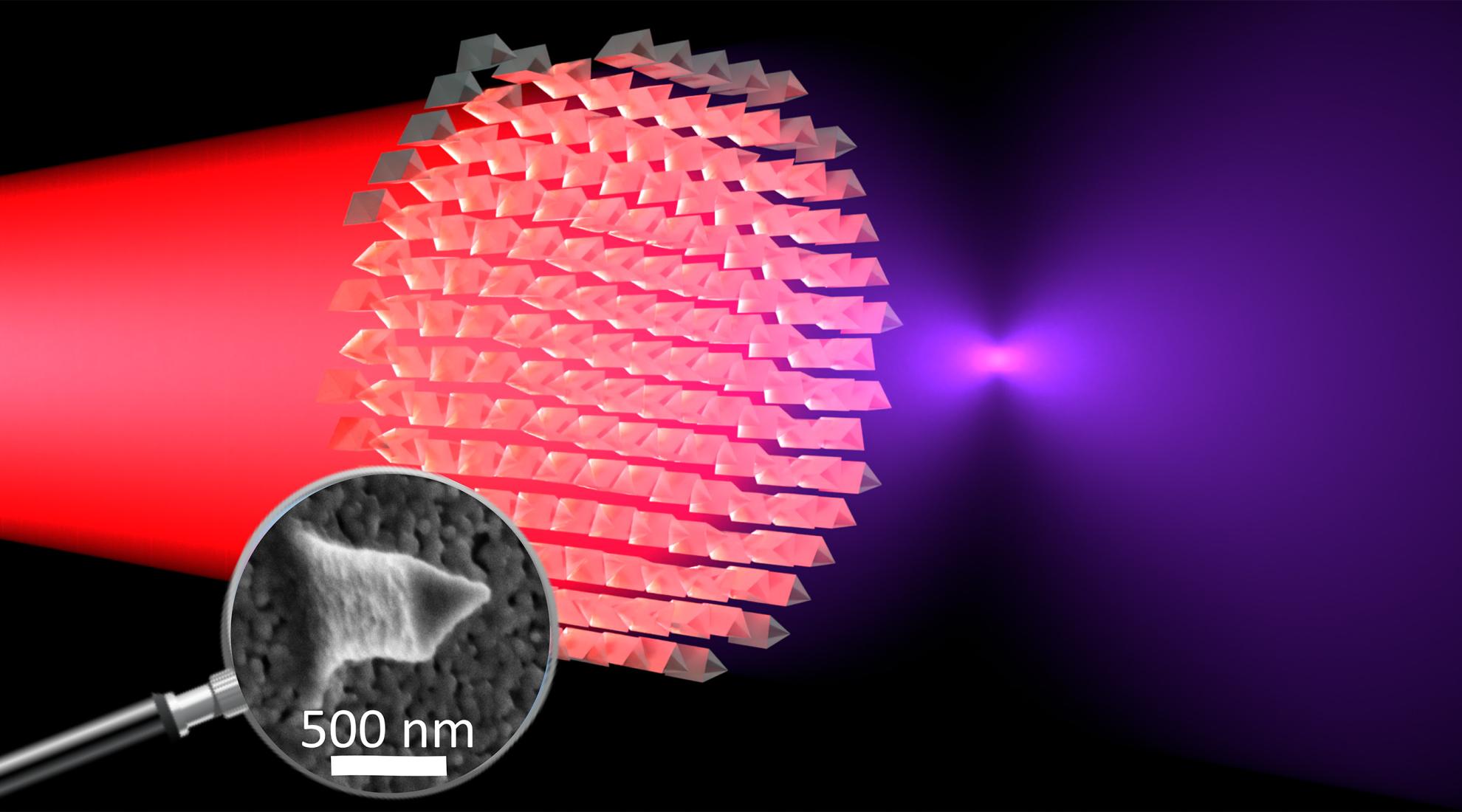
Thanks to an innovative manufacturing method, optical lenses can now be made not only significantly thinner, but also capable of converting invisible infrared light into visible light.
In recent years, photo cameras have evolved rapidly and become ever more compact – nowadays they are an essential part of every smartphone. But have you ever noticed that even in the thinnest phones, the camera lens still sticks out from the case? The reason lies in how conventional lenses work: they focus light to a single point to produce sharp images and videos. To achieve this, the lens needs a curved surface to refract the light correctly.
For the past decade or so, researchers worldwide have been working on the development of the metalens – a lens that, according to ETH Zurich, is practically flat and about 40 times thinner than a human hair. Unlike traditional lenses, which rely on curved glass to bend light, metalenses steer light using specially designed nanostructures on their surface.
Making infrared light visible
Being able not only to direct light but also to change its colour might sound futuristic, but it is quickly becoming a reality. A research team led by Professor Rachel Grange at ETH Zurich has developed a new method to produce ultra-thin metalenses from the crystal material lithium niobate. These lenses are not only tiny but also extremely powerful: they can transform invisible infrared light into visible light – and, according to ETH, with remarkable precision.
This process is based on a phenomenon known as nonlinear optics. It's already used in green laser pointers: infrared light passes through a special material and is converted into green light. Lithium niobate is particularly well suited for this – but also notoriously difficult to process. That’s where ETH’s innovation comes in.
Stamping the surface structure
The new method involves shaping liquid lithium niobate using a mould – similar to how printing presses once worked. When heated to 600 °C, the material becomes crystalline and gains the exact properties required. This makes it possible to produce nanostructures with high precision and efficiency – even in large quantities. The team presented this process in a recent study published in the journal Advanced Materials.
A game changer for multiple applications
What makes this development so special is that lithium niobate-based metalenses work like traditional lenses but can also change the colour of light. For example, if infrared light with a wavelength of 800 nanometres is passed through the lens, visible light with a wavelength of 400 nanometres emerges – sharply focused.
Potential applications are wide-ranging: from invisible security features on banknotes to simple camera detectors to make infrared light in sensors visible. While the technology is not yet ready for the market, its potential is immense.