Sustainable foam made from agricultural waste
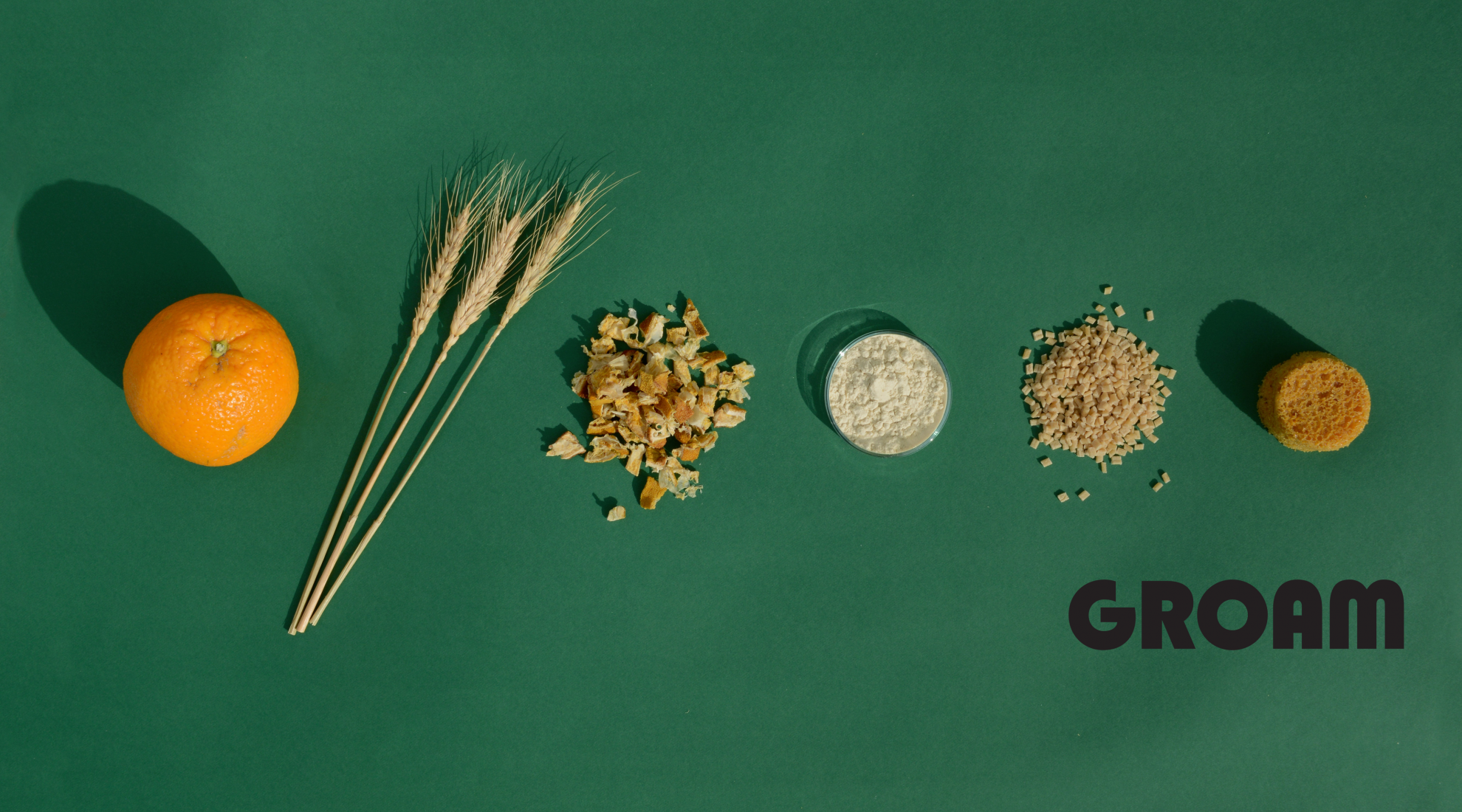
The Zurich-based start-up Groam intends to revolutionise the polymeric foam industry by developing more sustainable foam solutions. It uses a new proprietary foaming technology – inspired by food processing technology – to foam agricultural waste streams from fruit and cereal.
Polymeric foams are widely used in civil and industrial applications across sectors from construction to automotive, fashion or packaging. The global polymeric foams market is projected to reach 30 million metric tones by 2020 at a CAGR of more than 3.5% (Source: Polymeric Foams Structure-Property-Performance: A Design Guide, Bernard Obi). The main sectors in the polymeric foam industry are: construction, automotive, protective packaging, furniture, rail, wind, marine and others.
Unfortunately, most of these foams are made from petrochemicals, which later contribute to plastic pollution. At the same time it is a fact that roughly one third of the food that is produced globally is lost or wasted.
Biodegradable foam with Swiss technology
ETH start-up Groam is replacing conventional plastic foams with sustainable, biodegradable versions from agricultural waste streams from the fruit or cereal industries. Currently, the start-up from Zurich is working on foams, that can be used as root support system for indoor farming. To make such foams, Groam is developing a biodegradable material formulation, which is foamed with a novel foaming technology. Today, Groam is testing their foamed growth substrate with end-users. In the future, the founders plan to expand to biodegradable protective packaging for e-commerce and develop even more durable foams for the fashion industry.
From ice cream to sustainable foam
The co-founder of Groam, Dr Zuzana Sediva, developed the new foaming technology for food products such as ice cream during her PhD at ETH Zurich in 2019. Shortly after her doctorate, the idea of foaming food waste was born. The idea was to use this in the polymeric foam sector, where end products are hard to recycle and often still end up in landfill or being incinerated. The resulting products are a huge burden on the environment, because it takes decades for plastics to break down into micro-parts, and they never completely degrade. Products made from plastic foam are also very difficult to recycle. In 2020, Sophie Grimm, expert in materials and food processing joined Zuzana after her finishing her masters degree as co-founder. As of today, the team consists of three researchers.

Zuzana Sediva, founder and CEO of Groam.
Groam's solution is sustainable in two ways: first, the biomass it uses is a renewable resource and does not compete with food. It is highly abundant. Today to dispose large waste amounts, the waste often needs to be incinerated. The combination of the material and technology represents a novel green technology yielding biodegradable light weight materials. Groam is working on calculating the footprint of the process and comparing it to processes for fossil-fuel based polymeric foams. The technology is a green technology based on water and gas.
A USD 125 billion market is waiting
Groam wants to use its sustainable process to enter the growing market for polymeric foam, whose business volume is estimated to be USD 125 billion in 2021, according to Grand View Research polymeric foam report. Currently, Groam is advancing business development and product development to attract its first pilots before a planned seed round. The start-up is supported by various Swiss organisations such as Sitech4impact, Bridge proof of concept grant and ETH Zurich.