Maintaining medical supplies in conflict zones
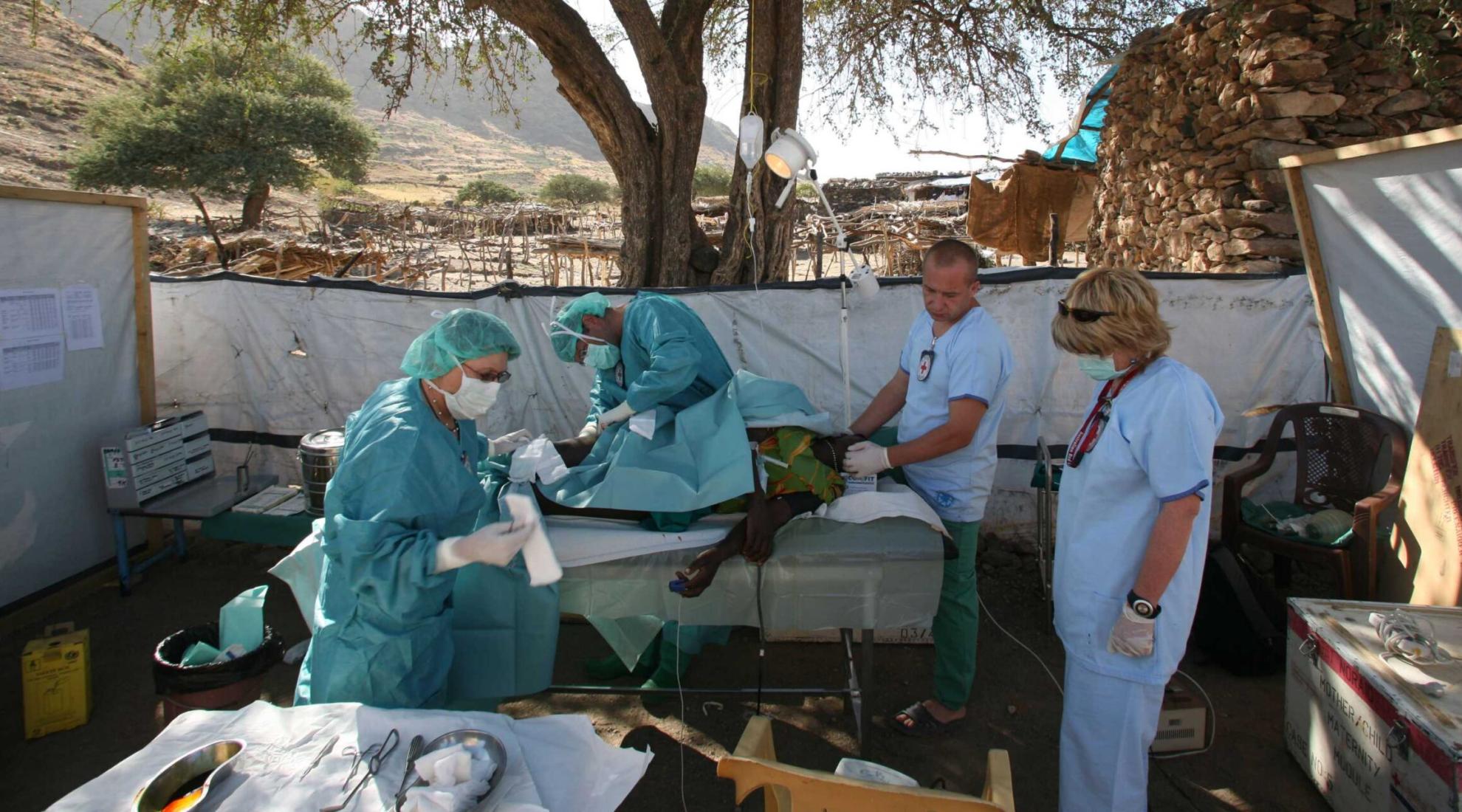
Stocking medical facilities, like this one in Sudan, is challenging for the ICRC’s logistics department.
Medical supplies are invaluable, especially in war and crisis zones. But getting them there is neither cheap nor easy. A new ETH Zurich tool for the International Committee of the Red Cross (ICRC) has made the process more efficient and cost-effective.
The ICRC is committed to helping people affected by war and conflict around the world. To enable medical personnel to provide first aid in the world's trouble spots, there must be no interruptions in the supply chain. In most cases, however, it is not as simple as ordering the required product from Amazon and having it delivered the same day. Having the wrong stocks on the ground can cost millions or, in the worst case, lives.
New logistics planning tool for medical supplies
Supplies usually pass through the ICRC's headquarters in Geneva and are then sent to logistics centres and warehouses before arriving in crisis areas. This requires a constant balancing act from the ICRC's logistics department. What is needed? How much? And where specifically? For some time now, an inventory calculator and special planning process have been helping staff perform this complex task. Both were developed by a team of researchers from ETH Zurich and the Chair of Logistics Management.
Stocks reduced by a quarter
In 2023, twelve sites in Africa, the Middle East and Ukraine were equipped with the tool, which was developed on the basis of a calculation method from logistics research. As a result, the ICRC was able to reduce its stock levels by 24% without compromising the quality of its supplies. A total of CHF 3.6 million was saved by reducing the amount of expired stock and the storage space required.
Addressing fluctuations in demand and delivery times
The ICRC's logistics staff were already using planning software. However, it turned out that this software was not very good at addressing fluctuations in demand for certain goods and their delivery times.
Thanks to our collaboration with ETH Zurich, we’ve discovered how strongly demand and delivery times fluctuate for different products. We were able to use the inventory calculator to determine the optimum balance between the desired supply level and the required stock level for each product.
Data as the basis for more efficient logistics
Since the new system was introduced, the planning of order quantities and stock levels has been based entirely on data and functions as a separate process. According to the researchers, the new system ensures a 98 per cent service level for items with reliable delivery times that are in constant demand. For goods with greater fluctuation in delivery times and demand, the ICRC aims to meet 85 per cent of demand immediately. Thanks to the planning tool, this is now reliably possible.
The logistics project is part of the Engineering Humanitarian Aid Action (EHA) initiative launched by ETH Zurich, EPFL and the ICRC in 2020. The three Swiss institutions are harnessing their combined expertise to support humanitarian action.