Artificial muscles from a 3D printer
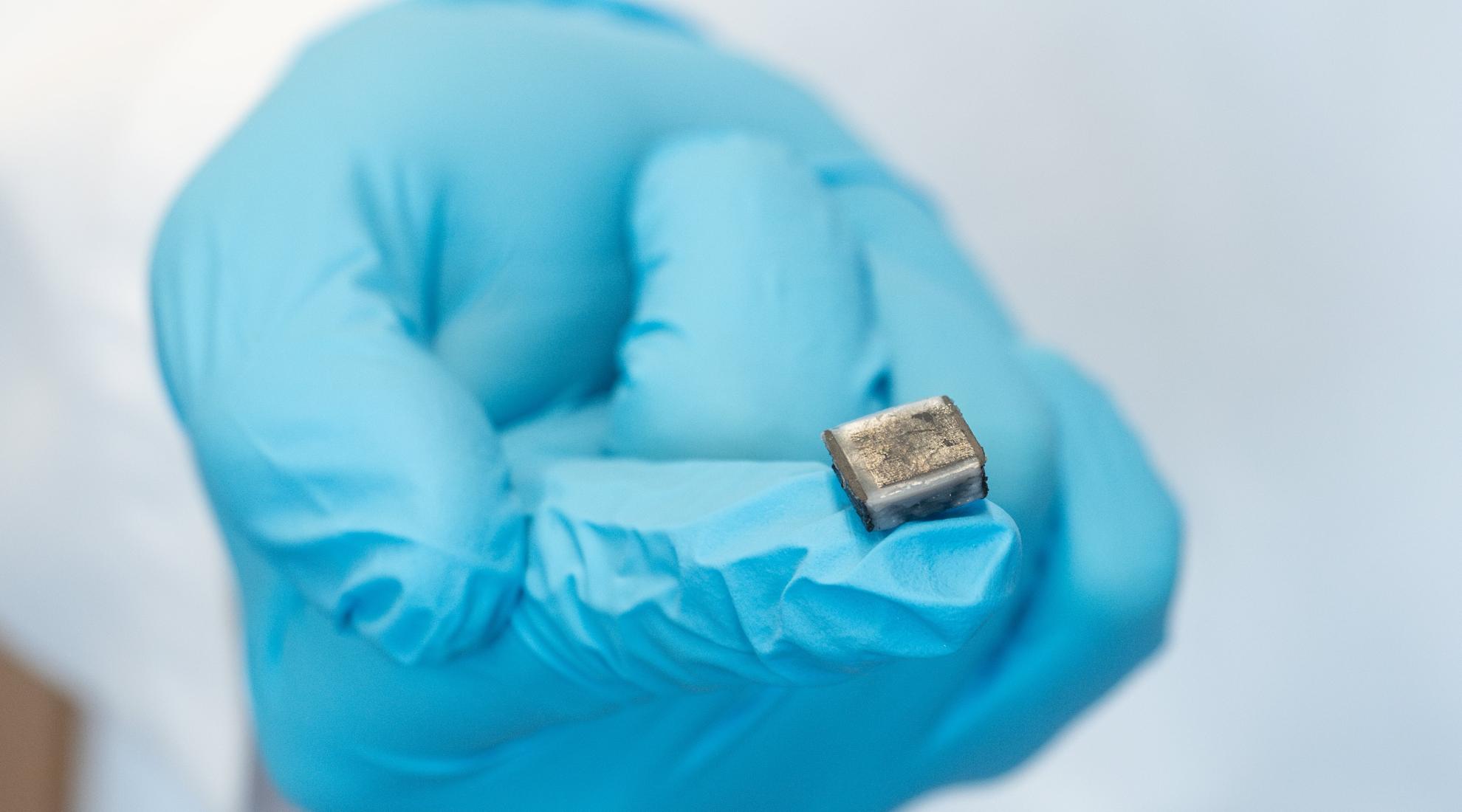
A 3D-printed artificial muscle from the Empa laboratory.
Swiss researchers are working on a method of printing silicone muscles that could be used in medicine and robotics.
Whether an entire heart in the human body will ever be replaced by artificial muscles from a 3D printer is still up in the air. However, a team of Empa researchers has taken an important first step by developing a new manufacturing method for producing artificial muscles from a 3D printer.
Elastic and soft
According to the Empa report, developing artificial muscles that are every bit as good as the real thing is a major technical challenge. To keep up with their biological counterparts, artificial muscles must not only be strong, but also elastic and soft. The development involves what are known as actuators – components that convert electrical impulses into movement. Actuators are used wherever something moves at the push of a button, whether in the home, in a car engine or in highly developed industrial plants.
Two silicone-based materials combined
The printed dielectric elastic actuators (DEAs) consist of two different silicone-based materials. A conductive electrode material and a non-conductive dielectric. When an electrical voltage is applied, it contracts like a muscle. When the voltage is removed, it relaxes to its original position.
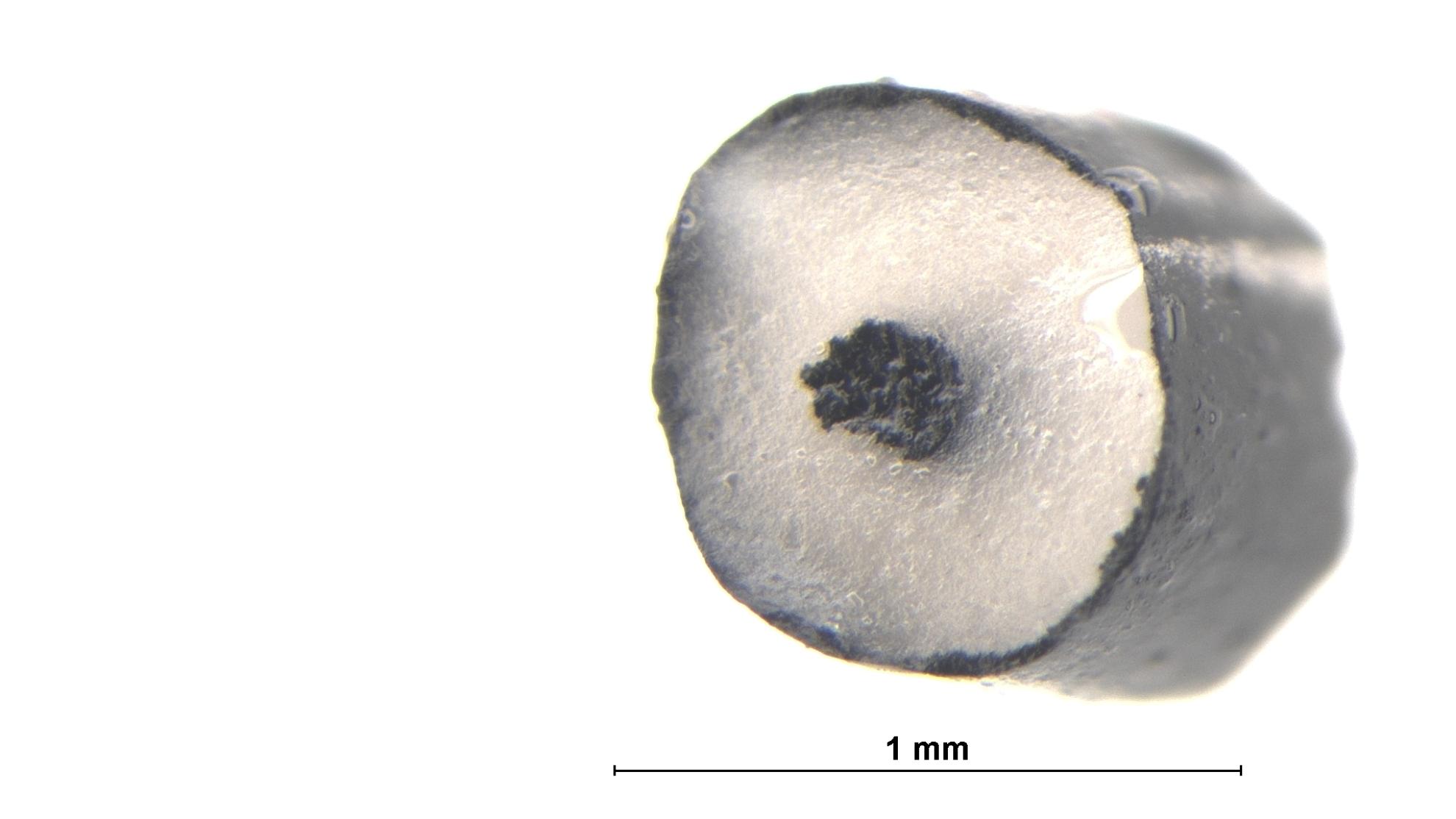
Microscopic image of the printed muscle fibre showing its structure.
The tricky part of the 3D printing process
As you can imagine, 3D printing is not an easy process. The two different materials must not mix, but still hold together well in the finished actuator. They also need to be as soft as possible so that they can harden when electrically stimulated. And, as with all 3D printing processes, the material must liquefy under pressure so that it can be pressed through the printer nozzle and then hardened back into the correct shape. In collaboration with researchers at ETH Zurich, as part of the large-scale project Manufhaptics, it has been possible to combine many of these contradictory properties.
If we manage to make them just a little thinner, we can get pretty close to how real muscle fibres work.
The soft actuators have many applications. They are lightweight, silent and, thanks to 3D printing, can be made in any shape. They could therefore replace conventional actuators in cars, machines and robotics. With further development, they could also be used in medical applications.